Reduce Risks at The Workplace and Avoid Getting Fines During Regulatory Supervision
Safety data sheets are an essential part of the safety work required to protect yourself and your employees when working with chemical products. You who sell chemical products classified as dangerous must, therefore, by law, provide safety data sheets to resellers and professional users.
The safety data sheet means to reduce risks that may arise by describing suitable protective equipment and how to act in the event of an accident. The SDS information needs to be up-to-date and delivered in the official language of the market where the chemical product is being sold.
However, having correct and up-to-date information on all your safety data sheets can be challenging as it requires a thorough routine and specially adapted work processes. And, if you lack correct safety information, the government can issue fines and withdraw permits.
But to help you, there are chemical management systems to ensure that your safety data sheet’s information is updated and correct. With these systems, you can keep track of all the chemicals in your business and easily access updated safety data sheets in different languages.
What Is a Safety Data Sheet (SDS)?
A safety data sheet is a digital or physical document bound to a specific chemical product that contains essential information to prevent harm to people and the environment. The document must comply with both national and European regulations.
All professional users and resellers must be able to access the safety data sheet quickly and easily per law. Both suppliers and EU importers are responsible for creating safety data sheets, which they then must keep up-to-date with the latest information. Requirements for when a SDS is to be provided are set out in Article 31 of REACH (Regulation (EC) No 1907/2006).
How to Translate and Update a Safety Data Sheet
Safety data sheets must always be kept up-to-date, following the latest regulations. This means that your SDS should be reviewed and updated as soon as new relevant information is published.
Companies that sell chemical substances or mixtures must provide previous customers with a new safety data sheet if an update is made within 12 months of purchase. It is also essential to save all SDS you receive or create for at least ten years, as you may need these during an inspection.
According to the REACH Regulation, the safety data sheet must also be translated into the language spoken on the market where the chemical product is being sold. For example, if you import chemical products into the Swedish market, you must deliver the associated safety data sheet in Swedish.
When is a Safety Data Sheet Required?
Safety data sheets are part of the strategic toolbox and signal quality to buyers as well as create security for suppliers. All companies that place a hazardous chemical product on the market must present a safety data sheet.
However, not all chemical products require a safety data sheet. Examples of these are medicines, food, and cosmetic products intended for end-users. Safety data sheets are also not required for hazardous chemical products designed for private consumer use.
You do not have to produce a safety data sheet if the product is not classified as dangerous and does not contain chemicals subject to reporting. However, creating a safety data sheet can be a great way to show users how to manage the chemical product safely, even if the document is not mandatory.
Updated Safety Data Sheets are Required for:
- Substances/mixtures classified as hazardous (e.g., flammable, oxidizing, explosive, hazardous to health, or hazardous for the environment) following Regulation (EC) No 1272/2008.
- Long-lived, bioaccumulative and toxic (PBT) substances/mixtures that are not classified as dangerous but contain low levels of allergenic substances.
- Substances included in the candidate list of substances for which authorization may be required under Article 59 (1) of REACH.
Updated Safety Data Sheets are Required for:
- Substances/mixtures classified as hazardous (e.g., flammable, oxidizing, explosive, hazardous to health, or hazardous for the environment) following Regulation (EC) No 1272/2008.
- Long-lived, bioaccumulative and toxic (PBT) substances/mixtures that are not classified as dangerous but contain low levels of allergenic substances.
- Substances included in the candidate list of substances for which authorization may be required under Article 59 (1) of REACH.
Who is Responsible?
The person who delivers the safety data sheet is responsible for the sheet’s content, no matter who the manufacturer is. Therefore, your role in the supply chain determines what obligations you have; these obligations are governed by Article 31 of the REACH Regulation.
The supplier information must be specified on the safety data sheet, regardless of whether you are a manufacturer or distributor. Therefore, the SDS must be updated with a complete address, telephone number, and e-mail address before send out.
As a distributor of chemical products, you must also ensure that the safety data sheets you distribute are correct. Due to this, you may need to update or translate the SDS information before send out.
As an employer, it is then your responsibility to ensure that the safety information reaches the employees who manage the chemical product. It is also your responsibility that the staff concerned can read and understand the information presented.
How and When Do I Send Out Safety Data Sheets?
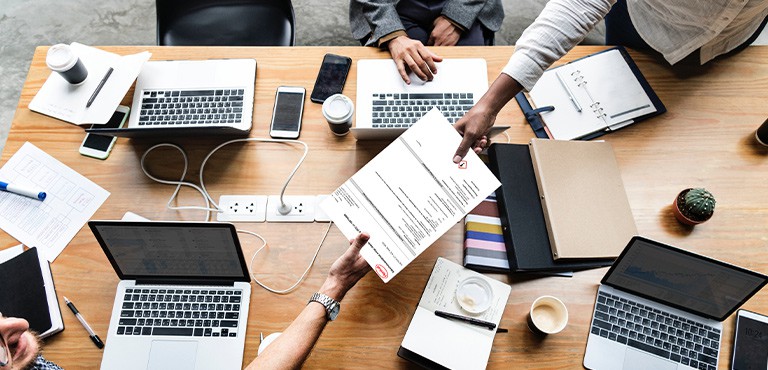
How to Read a Safety Data Sheet?
What Does a Safety Data Sheet Contain?
The safety data sheet has 16 sections whose headings, subheadings, and order are mandatory. The safety data sheet must be explicit, easy to read, and in the correct language.
The 16 Sections of a Safety Data Sheet
1. Identification of the substance/mixture and of the company/undertaking
In section 1, you will find the name of the substance/mixture and relevant identified areas of use. You will also find the supplier’s name and contact details together with a telephone number for emergencies.
If a substance has a registration number, it is noted here as well.
2. Hazards identification
In section 2, you can find the product’s classification and labeling combined with other hazardous properties, such as “risk of dust”.
3. Composition/information on ingredients
In section 3, the substance or components of the mixture are presented together with information on concentration (refers only to a mixture’s components), classification, and chemical identities.
4. First-aid measures
Section 4 provides first aid instructions for the main symptoms and effects – both delayed and acute.
It is vital that those who do not have medical training understand how to perform appropriate treatments and whether further medical treatment is needed.
5. Fire-fighting measures
Section 5 informs you on what is needed to fight a fire – including both suitable and unsuitable extinguishing agents (both those that have no effect and those that can aggravate the situation by, for example, reacting with the product).
You can also find information on whether fire-fighting personnel needs special protective equipment and whether the fire may risk unexpected hazards, for example, the formation of toxic carbon monoxide gas.
6. Accidental release measures
Section 6 presents recommendations for actions in the event of spillage, leakage, or discharge – and how to prevent, or minimize, the harmful effects on humans, property, and the environment.
You can also find information on personal protection, protective equipment, and emergency measures.
Reference to sections 8 and 13 if appropriate.
7. Handling and storage
Section 7 describes how to safely manage the chemical product, emphasizing protective measures appropriate to both scenarios mentioned in section 1.2 and specific properties of the substance/mixture.
Here you can find out how to store the chemical product in the safest possible way concerning, for example, corrosion, temperature, sunlight, and ventilation. Storage advice presented is based on the product’s characteristics described in section 9.
8. Exposure controls and personal protection equipment
Section 8 informs you of the applicable limit values and how you can limit exposure to the substance/mixture in the workplace. This includes a description of personal protection equipment such as eye protection, protective clothing, gloves, and respiratory protection – as well as information on when to use it.
9. Physical and chemical properties
Section 9 describes relevant physical and chemical properties, such as product color, odor, viscosity, pH, flash point, and freezing point. The classification ” corrosive ” may also be relevant to state in this section if the substance/mixture is strongly acidic or alkaline (pH≤2 or pH≥11.5).
Physical hazard classes that did not result in classification may also be appropriate to provide here, such as explosives, flammable gases, and self-reactive substances/mixtures.
10. Stability and reactivity
Section 10 mentions the stability of the product and the risk of dangerous reactions during specific conditions of use, as well as environmental emissions. You can, for example, find information on chemical stability, situations to be avoided, and incompatible materials.
11. Toxicological information
Section 11 holds information intended for medical staff, occupational health professionals, and toxicologists. Here is a brief but complete description of the toxicological effects together with source references.
This section informs on hazard classes that affect human health and information on effects and symptoms that may occur during probable routes of exposure. This includes both delayed and immediate effects as well as chronic effects of short-term and long-term exposure.
12. Ecological information
Section 12 describes chemical properties that may affect the environment during discharge together with data relating to toxicity, persistence, degradability, and bioaccumulation.
13. Disposal considerations
Section 13 lists suitable waste management options for both the chemical substance/mixture and possible packaging. This includes methods as, for example, incineration, material recycling, and landfill.
Here is also stated whether the leftover product classifies as hazardous waste.
14. Transport information
Section 14 provides classification information for transport by road, rail, sea, inland waterway, and air. Where relevant, transport classifications according to the following regulations for each type of transport must also be stated:
– ADR (road)
– RID (railway)
– IMDG (shipping)
– ICAO / IATA (flights)
The information in this section includes UN number, hazard class for transport, official transport name, and packaging group. In maritime transport cases where the IMDG Code covers the transported goods, the technical name must also be provided.
15. Regulatory information
Section 15 states whether the product is subject to additional EU regulations or national legislation. It also says whether the supplier has carried out a chemical safety assessment of the substance/mixture.
16. Other information
Section 16 has information not specified in sections 1-15. For example, previous changes made in the safety data sheet, explanations of concepts, source references, and explained abbreviations (unless they are presented in sections 2-15).
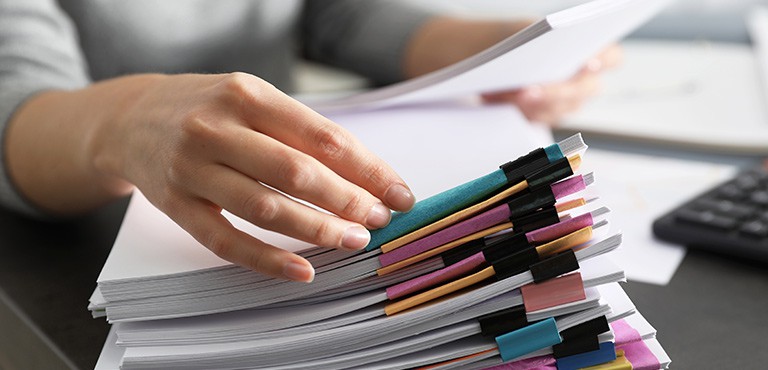
How and When to Use the Safety Data Sheet?
You should always review the safety information before managing the chemical product for the first time. However, safety data sheets are often very comprehensive, and in many work-related cases, safety documents are used instead of the safety data sheet.
Some of the information in your safety data sheet is probably irrelevant to your business; the safety document can therefore provide you with simplified and better tailored information. Nevertheless, all employees must have access to the complete SDS – even though they do not need to have read it (as long as the information is provided).
The safety information exists to protect you and the environment. Therefore, all who manage the product should be regularly updated on the latest information to stay informed about current risks and protection routines.
How to Store the Safety Data Sheet
The safety data sheet must be kept easily accessible to all that manage the chemical product. This can be done either digitally or physically. An advantage of storing the SDS digitally is that you are linked to the supplier and always have access to updated SDS.
Legislation and Regulations
Safety data sheets must be created following the CLP and the REACH (EC) regulations. These regulations state the requirements for the classification and the safety data sheet’s content.
In addition to EU legislation, national requirements are also often set for safety data sheets.
The REACH Regulation
REACH is an acronym for “Registration, Evaluation, Authorization, and Restriction of Chemicals”. According to the REACH Regulation, hazardous chemical substances must always have an associated safety data sheet.Annex II in REACH also contains explicit guidelines for creating safety data sheets and their sections and headings.
The CLP Regulation
The CLP Regulation holds the requirements for the classification, labeling, and packaging of chemical products. One of the primary purposes of the CLP Regulation is to ensure that hazardous chemical substances/mixtures are classified correctly, which is of great importance to protect both human health and the environment.
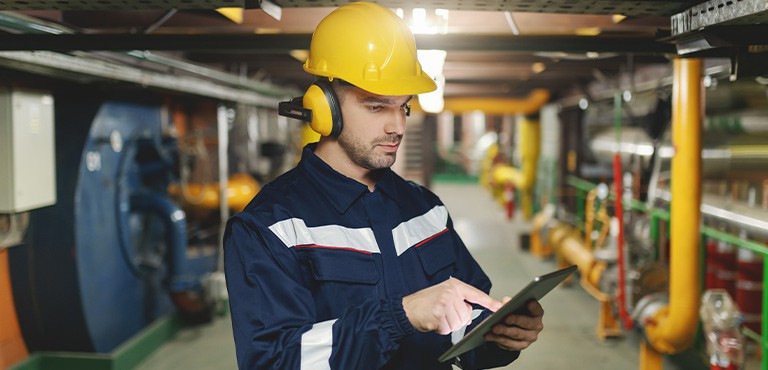
Frequently Asked Questions
What Products Do Not Need Safety Data Sheets?
You do not need to create a safety data sheet if the product is not classified as dangerous and does not contain reportable chemicals. Some end-user products do not require safety data sheets, such as medicines, foods, and cosmetics.
To Whom Do You Need to Provide Safety Data Sheets?
The safety data sheet must reach all professional users. Therefore, you must always attach a safety data sheet when delivering or selling chemicals or other chemical products. The safety data sheet must reach the recipient no later than the same day as the first delivery of the product.
Retailers must also be able to provide professional users with a safety data sheet on request.
How Often Do You Need to Update the Safety Data Sheet?
Current regulations do not specify how old a safety data sheet can be. However, a safety data sheet should be reviewed and updated regularly as the guidelines for chemical products in legislation and regulations are constantly changing.
For How Long Must the Safety Data Sheet be Available to the Customer?
The safety data sheet must follow the chemical product from manufacture to end-user (except retail and private consumers) and must be available on request for at least 10 years.
We Simplify Your Work With Safety Data Sheets
Our EHS consultants have extensive experience working with safety data sheets and are happy to help you review, translate, and create new safety data sheets for your chemical products.
If you want to streamline and simplify the use of your safety data sheets, contact us directly and we will tailor a solution. Email us at consulting@intersolia.com
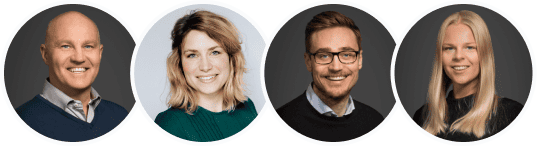