Protect Your Employees by Identifying Chemical Hazards in The Work Environment
Everyone who manages chemicals should be aware of the risks that are involved. To ensure a safe working environment, employees must have sufficient information about the chemicals and how to protect themselves. To do this, you need risk assessments.
Without active risk assessment work, illnesses and accidents can have severe consequences for the company in the form of lost production, absent workforce, and damaged equipment. It is therefore of great importance, and a legal requirement, to carry out risk assessments regularly and systematically.
A faulty or ignored risk assessment can lead to unnecessary chemical exposure that can cause allergies, cancer, and other serious health problems.
Our knowledgeable EHS consultants have extensive experience guiding companies in the risk assessment process to create safer work environments and sustainable operations.
Do you want to know how we can help you with your risk assessments? Contact us directly below.
What Is a Risk Assessment?
“Risk” means the probability of illnesses or accidents happening and the consequences that follow. A risk usually depends on how things are organized, in combination with human and technical factors. Risk assessments are about being one step ahead, a way of preventing accidents that have not occurred.
With the help of a risk assessment, you map out your work environment and review different risk scenarios. The risk assessment is then conducted, documented, and followed by an action plan.
In addition to being an excellent tool for day-to-day work, risk assessments are essential to show during supervision by authorities.
Risk Assessments When Working With Chemicals
Risk assessments are carried out in all industries, and several of them include chemical management. But there are different requirements for mapping risks when working with chemical products, and the REACH legislation (EU) and other relevant national laws often set different demands.
Therefore, what risks you should assess when working with chemical products depends on both the exposure scenario and chemical properties.
There are several ways to keep people managing chemicals informed, for example, via the product’s safety data sheet or label. But none of these include the risks that can arise in specific work situations. Therefore, you need risk assessments to ensure a safe working environment.
The purpose of a risk assessment is to ensure that the protective measures taken are sufficient – or if there is a need for further actions. The assessment includes how, when, where, and for how long exposure to the chemical substance occurs. But it also looks at, among other things, ventilation, first aid equipment, and waste management.
When and How Often Should You Carry Out a Risk Assessment?
When the risks in your business are considered severe – risk assessments must be carried out and documented. However, the rule of thumb is to conduct a risk assessment when there is a work scenario where employees are exposed to risks – regardless of business size or severity.
You should always carry out new risk assessments when something changes in the business or the management of the chemical. This change can include, for example:
- Change in working methods or working hours
- New or updated work equipment
- Substitution of a product or chemical
- Renovations or new constructions
A risk assessment is not something you perform only once, but continuous work where you return annually (or as often as the specific scenario requires) to see if further actions are needed – or if current measures are redundant.

How to Carry Out a Risk Assessment
So, how do you conduct a risk assessment? Several components are essential for the risk assessment to be done correctly. This chapter looks at who is responsible, what chemicals and scenarios should be risk assessed, and what the risk assessment itself should contain.
Who Carries Out the Risk Assessment - and Who is Responsible?
The employer is responsible for ensuring that the risk assessments are carried out correctly. However, this does not mean that the employer must conduct the risk assessments as the employer can delegate this task to other staff.
However, it is crucial that this new person understands, and has approved, the responsibility and what it entails.
We recommend you create the risk assessments in collaboration with the employees who handle the chemical product – as they can best describe the methods used when working with the product. It also facilitates the evaluation work and confirms whether the current protective measures are being followed and how well they work.
If necessary, the workplace’s safety representative can also participate in the risk assessment work together with an expert consultant – if, for example, you need specific measurements.
What Should Be Risk Assessed?
You should conduct risk assessments for all hazardous chemical products. But you can also conduct risk assessments for unclassified (seemingly harmless) products to ensure that there are no risks and that the products are actually harmless.
However, it is not only chemicals that can be risk assessed. Risk assessments should also include scenarios where other risks occur, even if the dangerous component is not the chemical.
Examples of these situations can be:
- Heating of liquid
- Demolition work
- Chemical reactions
- Work such as welding and soldering
- Slippery surfaces
Depending on how the chemical is used and treated, risks with, for example, gases or dust can also arise. That is why you need to be thorough in your risk assessment work, as you do not want to miss any unexpected scenarios.
What Should a Chemical Risk Assessment Include?
For work with chemicals, a risk assessment should include information on: Potential risks (examine), The risks found sorted according to severity (risk assessment), Action plan with appropriate measures (action), Control of taken measures and whether they have worked (verify).
Do not forget that the risk assessment is only valid when signed by the person responsible. It is also crucial that it is clearly written on the risk assessment document who made the assessment. You should then store the information on the premises to which it relates.

Quality Checking Your Risk Assessment - Was It Good Enough?
You can conduct your risk assessment in several different ways. You can either do it yourself, together with employees – or in collaboration with an expert. The only important thing is that you gather relevant information about the chemical management scenario and the best ways to address the risks.
But when you have carried out your risk assessment, how do you know if it was good enough?
Checklist: Evaluate Your Risk Assessment
1. Is the risk assessment up to date?
The risk assessment is relevant if you still use the same chemical product and manage it in the same way.
2. Are there any risks of skin contact or oral ingestion?
Including, for example, smoking or eating without washing your hands.
3. Is there a risk of vapor inhalation?
If so, measure air pollution to ensure that you do not exceed limit values.
4. Have you included information on previous accidents, occupational injuries, or other incidents?
Do not forget to include this information in the risk assessment.
5. Did you include the employees who manage the chemical products when conducting the risk assessment?
The personnel who handle the chemical product possess crucial knowledge regarding the actual management and possible unexpected risks.
6. Have appropriate measures been planned or implemented?
The risk assessment has probably resulted in several measures. It is of great importance that these are planned, carried out, and followed up.
7. Is the risk assessment signed and documented correctly?
You must document the risk assessment, and it must be clearly stated who has signed and approved it.
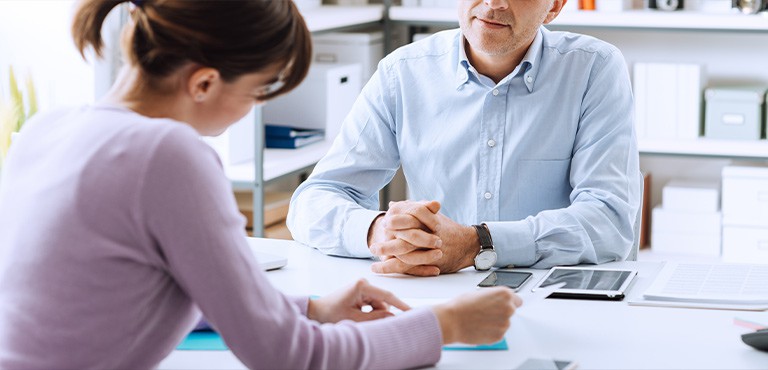
What Happens When You Have Completed the Risk Assessment?
When the risk assessment is documented and signed, you should store it where the risk is located. The risk assessment must then be easily accessible for all affected workers.
Depending on the result of the risk assessment, you must now carry out the appropriate safety measures. This could include, but is not limited to, new protective equipment, improved ventilation, and substitution of hazardous chemical products.
Depending on the risk scenario, you must then check the risk assessment and decided measures at an appropriate interval. But, you should do it at least once a year.
When reviewing the risk assessment, you should check everything in the checklist above. If you cannot check of the items on the list – you should conduct a new risk assessment.
Laws and Regulations That Apply to Chemical Risk Assessments
Frequently Asked Questions
Question 1. What is the Difference Between a Risk Assessment and a Risk Analysis?
The risk analysis is part of the risk assessment. The risk analysis includes risk identification. When the risk analysis is done, the assessments together with measures and action plan follow.
Question 2. Does it Matter Who Signs the Risk Assessment?
Yes, the person responsible for the risk assessment is the only one that can sign the document.
Question 3. Do Safety Representatives Have to Take Part in Risk Assessments?
No, but the safety representative can ensure that the employer carries out relevant risk assessments at the workplace.
Question 4. Who Should Participate in the Risk Assessment?
All parties who possess relevant information about the source of risk (for example, those who work with the chemical product), responsible personnel, and an expert if needed.
We Will Help You With Your Chemical Risk Assessments
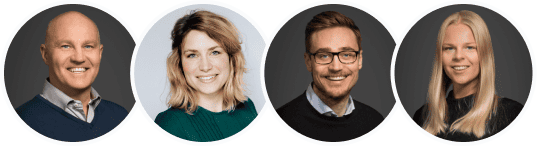